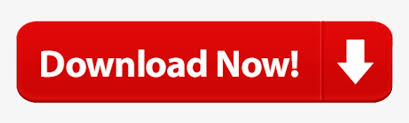
The world’s fattest countries: how do you compare? – Telegraph.
#Error 766 solidthinking inspire iso
Iso: ISO 10328: Prosthetics-Structural testing of lower- limb prostheses-Requirements and test methods, vol. 12, 77–89 (2016)Ĭanfit 3D CAD Prosthetic and Orthotic design software. 93(1–4), 467–479 (2017)Ĭhen, R.K., Jin, Y., Wensman, J., Shih, A.: Additive manufacturing of custom orthoses and prostheses-a review. Primo, T., Calabrese, M., Del Prete, A., Anglani, A.: Additive manufacturing integration with topology optimization methodology for innovative product design. Larsson, R.: Methodology for topology and shape optimization: application to a rear lower control arm (2016)Ĭlausen, A., Aage, N., Sigmund, O.: Exploiting additive manufacturing infill in topology optimization for improved buckling load. Walton, D., Moztarzadeh, H.: Design and development of an additive manufactured component by topology optimisation. Robbins, J., Owen, S.J., Clark, B.W., Voth, T.E.: An efficient and scalable approach for generating topologically optimized cellular structures for additive manufacturing. Panesar, A., Abdi, M., Hickman, D., Ashcroft, I.: Strategies for functionally graded lattice structures derived using topology optimisation for additive manufacturing. In: Solid Freeform Fabrication Symposium, pp. et al.: The BCC unit cell for latticed SLM parts mechanical properties as a function of cell size. Tang, Y., Zhao Y.F.: Lattice-skin structures design with orientation optimization. 174 (2010)ĭong, G., Wijaya, G., Tang, Y., Zhao, Y.F.: Optimizing process parameters of fused deposition modeling by Taguchi method for the fabrication of lattice structures. Sundararajan, V.G.: Topology optimization for additive manufacturing of customized meso-structures using homogenization and parametric smoothing functions, p. Rozvany, G.I.N.: A critical review of established methods of structural topology optimization. Siva Rama Krishna, L., Mahesh, N., Sateesh, N.: Topology optimization using solid isotropic material with penalization technique for additive manufacturing. Finally, the strength of the resultant prosthesis was validated through a compressive testing experiment. Also, the exoskeletal shape of the tibial region of the leg was maintained. Fatigue analysis was carried out for both scenarios. These cases were compared regarding the strength–weight ratio. Two case studies were considered, wherein the geometry was first optimized through conventional topology, and then the resultant geometry was further developed with a lattice. The consequent optimization was done in solidThinking Inspire. The subject’s leg was scanned, and the obtained geometry was simplified using ANSYS’ SpaceClaim. To fully exploit the advantages of this process, topology optimization was implemented on the geometry. Conventional manufacturing processes are not economical when dealing with a customizable prosthesis, so the newer technology of additive manufacturing is considered in this study. Fabrication of artificial limbs is a challenge since the shape and size of each prosthesis is different, and they have complex geometries. The need for artificial limbs or prostheses has been on the rise due to army personnel being injured in recent conflicts, an increase in the numbers of senior citizens, and road accidents.
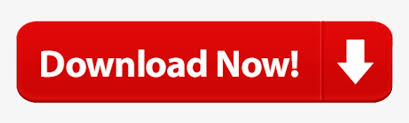